Soft Infrastructures for Reindustrialization: The Need for Tools to Help Reshoring
The primer of a longer series talking about the soft infrastructures that are needed for reindustrialization. As the U.S. seeks to rebuild its manufacturing base, a critical but often overlooked factor is the "soft infrastructure" that supports industry transformation. While physical facilities and policies are getting attention, the connective tools and systems, like data platforms, scenario planning, and real-time insights, are just as essential to smoothing the reindustrialization process.
Ethan Copple
4/8/20253 min read
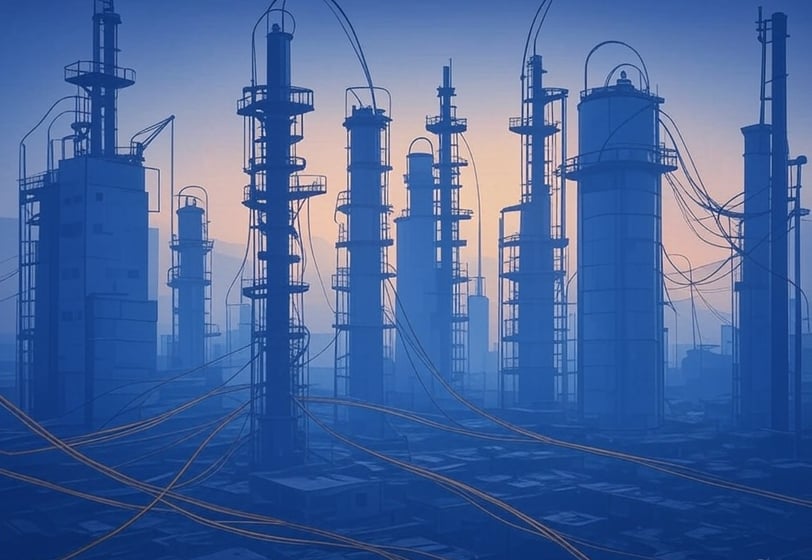
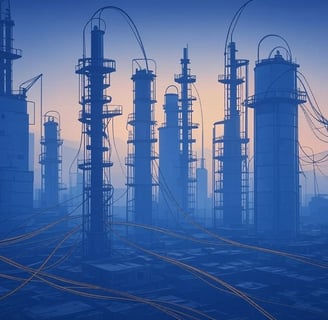
The Midwest is dotted with quiet giants, corrugated metal buildings in small industrial parks. Though unassuming, it’s safe to assume the work done in these buildings is in the tens if not hundreds of millions of dollars a year. One crisp Kansas morning, I stood outside one of these buildings. It looked like any other, but this one wasn’t a massive production site — it was a modest, regional R&D hub, quietly supported by both university and private funding.
What led me there was a shirt — and a conversation.
Wearing my Reindustrialize shirt around town, I was stopped by an older man. “Reindustrialize… what does that mean?” A quick conversation later, he passed me his business card, told me to add a few other people on LinkedIn, and told me to tour a little known research factory just 10 minutes from my home. A few DMs later and I scheduled a visit to tour and learn about the work done.
During the visit, I explained how I’d met people in the local manufacturing scene, the story behind the shirt, and the broader movement. One person remarked, “Never heard of it. Is it new? I feel like people have wanted to do something like that for years — but no one really had the time or power to change things.”
That’s the quiet truth I’ve seen again and again — in conversations with factory veterans, ops leaders, and engineering faculty. There’s a real hunger to build something new, but also a pervasive unawareness of the momentum already forming: national policy shifts, investment interest, renewed energy for domestic industry..
This unawareness, though not particularly surprising, points to a general ‘infrastructure’ issue facing reindustrialization. In this case, infrastructure is not referring to the electrical grid capacity, zoning laws, etc. but rather the soft infrastructures - the tendons and ligaments that allow the movement to collaboratively advance.
The official Reindustrialize Summit, New American Industrial Alliance, and related groups have been a spectacular start to this soft infrastructure, especially in relation to policy and politics. But when it comes to reshoring decisions, shifting supply chains, or increasing capacity on the ground, there are still big gaps.
Manufacturer websites are often outdated. Capabilities aren’t clearly listed. Quotes take weeks, lead times stretch into months, and sourcing departments are often flying blind — relying on outdated networks and incomplete data. On top of that, SMBs are increasingly expected to be amateur economists and geopolitical risk analysts, just to manage exposure and pricing.
Even when a company wants to reshore, or lean into the momentum, the practical next steps aren’t obvious.
Where can they turn for guidance? Consulting and SaaS have a bad rep in the world of atoms (and for reasonably good reasons), though something that can provide these big picture summaries, calculations, and plans is necessary.
We need more connective, soft infrastructure to smooth and quicken the process of Reindustrialization.
Imagine a tool purpose-built to empower U.S. manufacturers, supply chain leaders, and procurement teams with the insights they need to confidently bring production and sourcing closer to home. Not just another dashboard or data aggregator, but a comprehensive platform that integrates supplier networks, pricing, capacity, geopolitical risk, and logistics data, enabling scenario planning at a glance. A system that answers not just where something can be made, but why here, why now, and at what cost and benefit.
Instead of cobbling together spreadsheets, PDFs, and hearsay, imagine SMBs navigating this transformation with real-time intelligence: reshoring costs versus offshore risks, lead time tradeoffs, and regional capability mapping, all aligned with their operational realities and long-term strategies. In this vision, even small manufacturers can act with the confidence and precision of major primes.
Because the stakes have never been higher.
Supply chain fragility is no longer an abstract risk discussed in academic papers or niche conferences. It’s a tangible, recurring threat to economic security, business continuity, and national resilience. COVID-19 was not a one-off event; it was a warning shot. The ripples of geopolitical tensions, raw material scarcities, and shifting alliances will only grow more intense and unpredictable.
The question is no longer should we reindustrialize—it’s how quickly and effectively we can do it. And whether the right connective infrastructure exists to support that acceleration.
To close the gap between bold ideas and practical execution, we need more than vision and policy. We need infrastructure, not just in roads and factories, but in intelligence, networks, and digital systems that help translate national priorities into operational action. The time to invest in this connective tissue is now.